What is the Difference Between SOPs and Work Instructions?
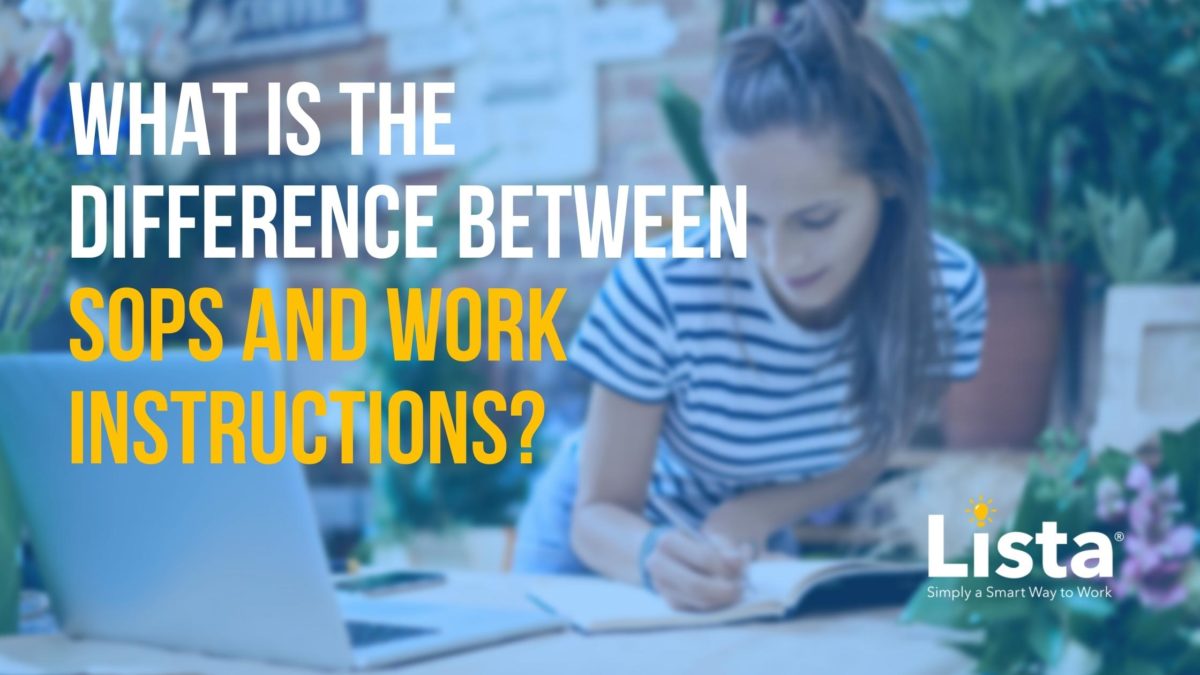
At first SOPs (Standard Operating Procedures) and Work Instructions might seem like synonyms – after all, aren’t these both standardized descriptions for how employees should carry out a particular task? Well, yes and no.
While it is true that these are both mandatory sets of instructions, they stand at different points in the hierarchy of documentation for process-driven business needs. SOPs are on top – high-level processes that you can follow even when some of the details change. For instance, you might move offices or factories, change out one machine for another, but the SOPs would likely remain the same.
By contrast, Work Instructions are very detailed descriptions which in theory could enable an inexperienced employee to perfectly carry out a task. Work Instructions must be kept up to date to align with even small changes in working practices, machinery, work location and other factors.
Let’s look a little more closely at both terms and the purposes these types of documented processes fulfill in the workplace.
Standard Operating Procedures
SOPs are high-level procedures that outline what to do under various circumstances. Here are some examples of SOPs you might have:
- An SOP for how to recruit new employees.
- An SOP for how to prepare and distribute monthly reports.
- An SOP for how to prepare and submit a government-required filing.
There is no need for SOPs to go into exhaustive detail because the principles, or core procedures, are applicable in a variety of settings and the expectation is that the employee will generally know how to effectuate each procedure across various circumstances.
The purposes of SOPs are many:
- They ensure consistency across an organization’s different departments and locations.
- They ensure that the company’s best practices are being followed.
- They reduce errors.
- They help ensure compliance with health and safety requirements, company policies, etc.
- They improve efficiency by negating the need for employees to ask what their next task is in any given scenario.
Work Instructions
Work Instructions, by contrast, are highly granular, detailing exactly how a particular procedure should be carried out. Work Instructions might hang on factory walls adjacent to the machines they refer to or be contained in a file that must be kept close at hand for referral where necessary.
Like SOPs, Work Instructions have a range of useful functions:
- Reinforcing safety procedures and preventing accidents.
- Improving efficiency and eliminating or reducing errors.
- Helping in the transmission of knowledge between team leaders and workers.
- Allowing managers to assess the quality of work being carried out.
Here are a few examples of Work Instructions:
- A Work Instruction detailing how to perform safety checks on a particular machine.
- A Work Instruction describing how to change the ink in a color copier.
- A Work Instruction providing the script for a customer support call.
SOPs and Work Instructions as Working Documents
Both Standard Operating Procedures and Working Instructions should be subject to regular evaluation and review. However, even here, there are potential differences in how this might be done.
While both SOPs and Work Instructions may be updated at any time, it is more common for SOPs to be re-evaluated at set intervals, perhaps quarterly, unless a sudden change is required by new legislation compliance regulations, a change in management, or an adverse event.
Work Instructions should ideally be reviewed more often and be under frequent revision, updated whenever a better, safer, or more efficient way of working is discovered. To make this easier, it helps for both SOPs and Work Instructions to be developed in a digital platform that is accessible and easy to use for to all, but mainly for those the staff workers and managers directly enacting the Work Instructions and SOPs.
When new Work Instructions are written or existing ones rewritten, it can be a process of ongoing improvement. In other words:
- First, observe how activities are currently undertaken.
- Ask staff and team leaders if this is the maximally efficient method.
- Break down the task into stages and write clear instructions for each step.
- Use visual aids such as diagrams, photos, and flowcharts when helpful.
- Next, show a draft Work Instruction document to all staff working with the procedures.
- Revise this draft accordingly before achieving a final sign-off from all parties.
- Finally, record the Work Instruction and link it to its appropriate SOP (if applicable).
Use an Online Platform for SOP and Work Instruction creation, revision, communication, and retrieval.
While the process of constructing the perfect SOP or WI might seem labor-intensive and complicated, fortunately, there are tools to make it easy!
A good business process management software allows you to create workable SOPs and Work Instructions in minutes, share them with the relevant colleagues, and track their uptake and adherence when used by employees. Because the level of complexity of some software platforms can be a barrier to adoption and use, it is important to find one that is easy to understand and implement.
Lista was developed specifically for small business owners and managers who want a tool that is easy to learn, easy to use, and has minimal training time for staff. Lista users report improved efficiency, communication, and accountability among other benefits.
“I found that Lista was straightforward to use compared to other products. Lista was easy to use, easy to figure out, easy to create procedures, and straightforward to see the steps and edit them; once I had decided what was going into the procedure it only took about 5-10 minutes to actually build it.”
Amanda Singer, Co-Founder
West Coast Family Mediation Center
If you are considering solutions to improve your business with SOPs and Work Instructions be sure to consider Lista! Lista offers a FREE 14-day trial, so you can try it out and quickly develop your own SOPs and Work Instructions to make your business more efficient and improve your bottom line.
Click HERE to sign up for your free trial today.
Creating & Editing Processes Made Easy
Our solution allows you to be more organized, efficient, and productive. Minimize learning time with easy-to-use software.
Start Your 14-day Free Trial Today